Optimizing Business
Performance
Organizational
Development and
by Leadership
We implemented leadership training programs and
designed an
organizational
development plan to enhance
team collaboration.
Company faced low employee engagement and leadership
challenges that
were
affecting overall performance.
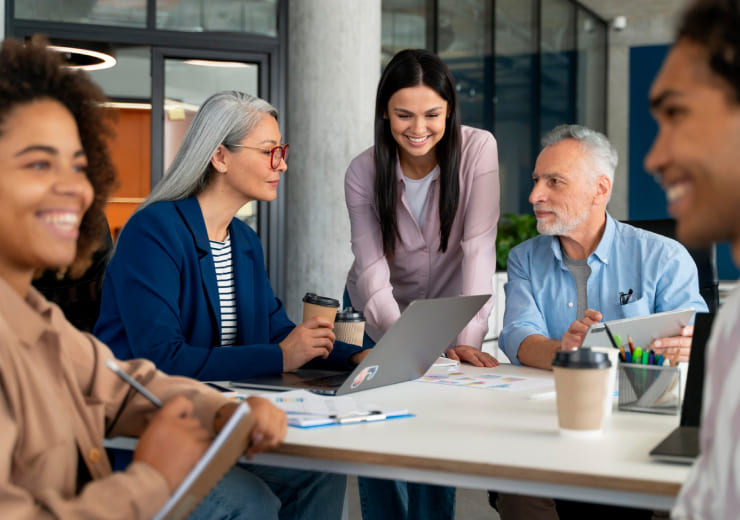
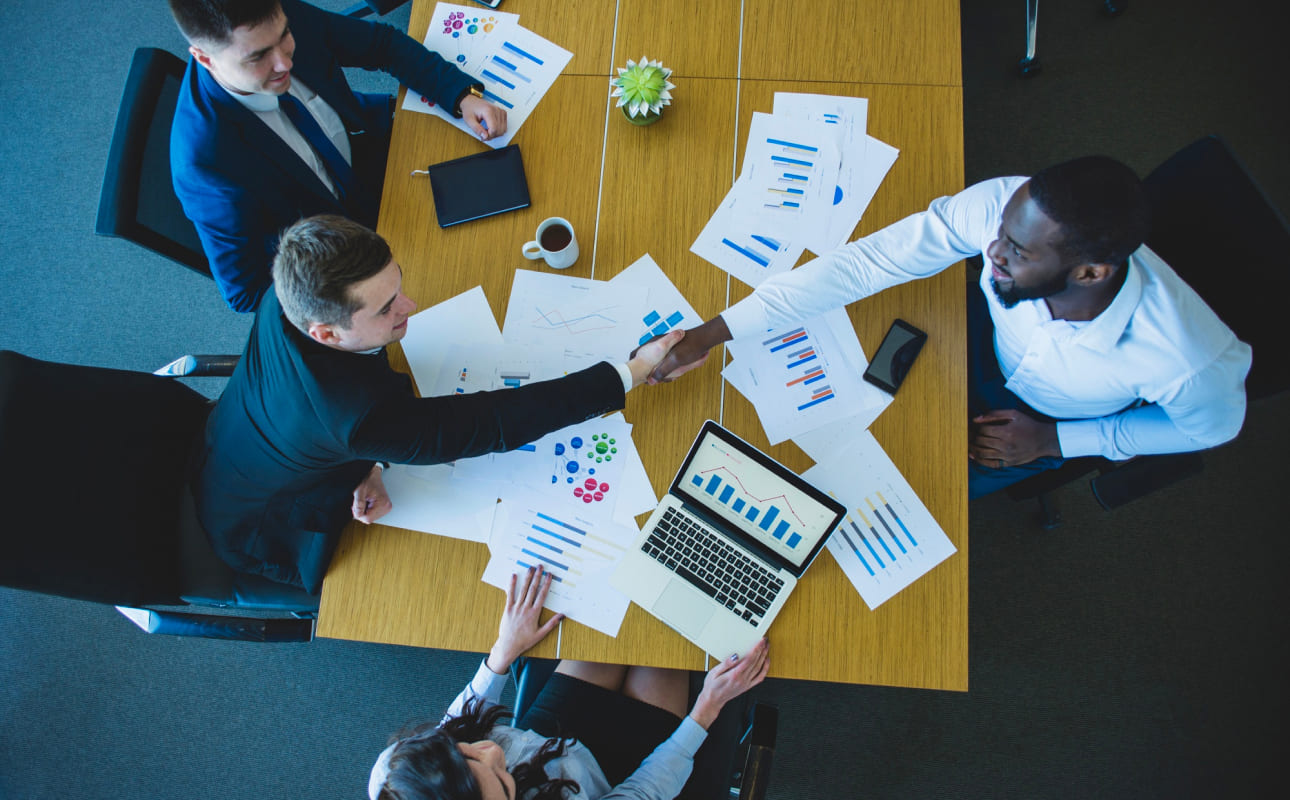
The Project Story
After conducting an initial assessment of ProTech Industries' operations, we identified several bottlenecks in their supply chain and production processes. Key issues included overstocking raw materials, misaligned production schedules with demand forecasts, and outdated technology that hindered real-time decision-making.
The Challenge
A mid-sized manufacturing company, ProTech Industries, was experiencing rapid growth, but their operational inefficiencies were starting to impact productivity and profitability. They faced challenges in supply chain management, production scheduling, and inventory control, leading to increased lead times, higher costs, and customer dissatisfaction. The leadership team sought a business consulting firm to assess and optimize their operations for scalability and sustainable growth.
The Results
We recommended the integration of an ERP (Enterprise Resource Planning) system that would automate and connect all departments—production, supply chain, and finance. Our team worked closely with the company to implement the system and provided training for staff to ensure smooth adoption.
Production Efficiency
Increased by 30%, allowing the company to meet growing customer demand without additional labor costs.
Inventory Costs
Were reduced by 20% due to better demand forecasting and the implementation of JIT supply chain processes.
Lead Times
Were shortened by 40%, leading to faster order fulfillment and they improved customer satisfaction.
Technology Integration
Provided leadership with real-time insights into operations, enabling more informed decision-making and allowing them to adjust